The first file is used to test the overhang limits and capabilities of the Ultimaker 2 3D printer, which i am going to use for this week assignment. The filament type is PLA.
This was what it looks like in Cura
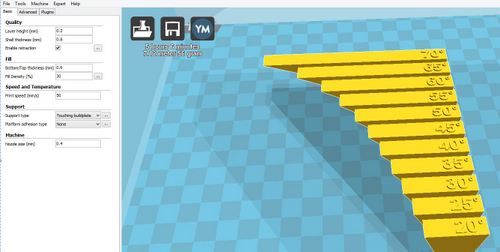
Overhang Angle Test Print
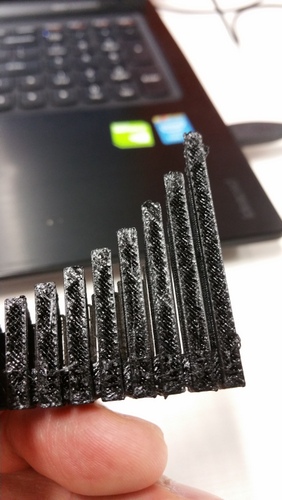
Actual Overhang Test Print
From the actual print you can observe 60 degrees overhang would still give you a good print without support. Printing at 70 degrees already starts to give problem. Printing above the 70 degree threshold without support would certainly failed the printing.
The second file is used t test the capabilities of the Ultimaker 2 printer.
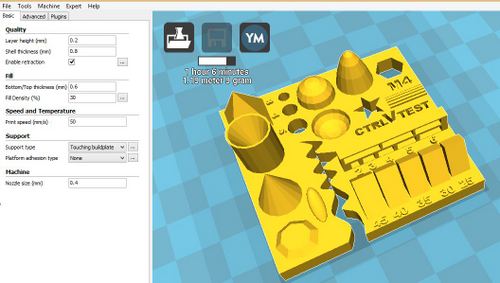
3D Printers Test
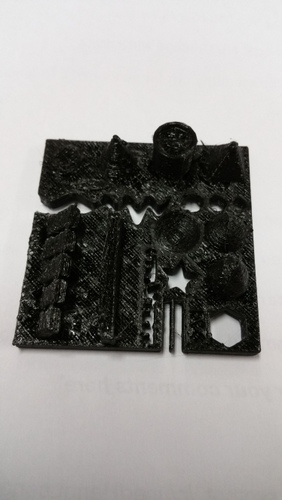
Actual 3D Printer Test
The informtion from these 2 prints let me get acquainted and gave me a better picture of the limits of the 3D printer and how should the product be design.
I came across this website STL Finder quite useful. (Hover over it, right click and click Open link in new tab). It contains plently of STL files of different shapes and sizes to help you test run your 3D printers.